Porosity in Welding: Identifying Common Issues and Implementing Best Practices for Avoidance
Porosity in welding is a prevalent concern that usually goes undetected up until it causes significant issues with the honesty of welds. In this discussion, we will certainly discover the essential factors adding to porosity formation, analyze its destructive results on weld performance, and talk about the ideal practices that can be embraced to lessen porosity event in welding procedures.
Usual Reasons of Porosity
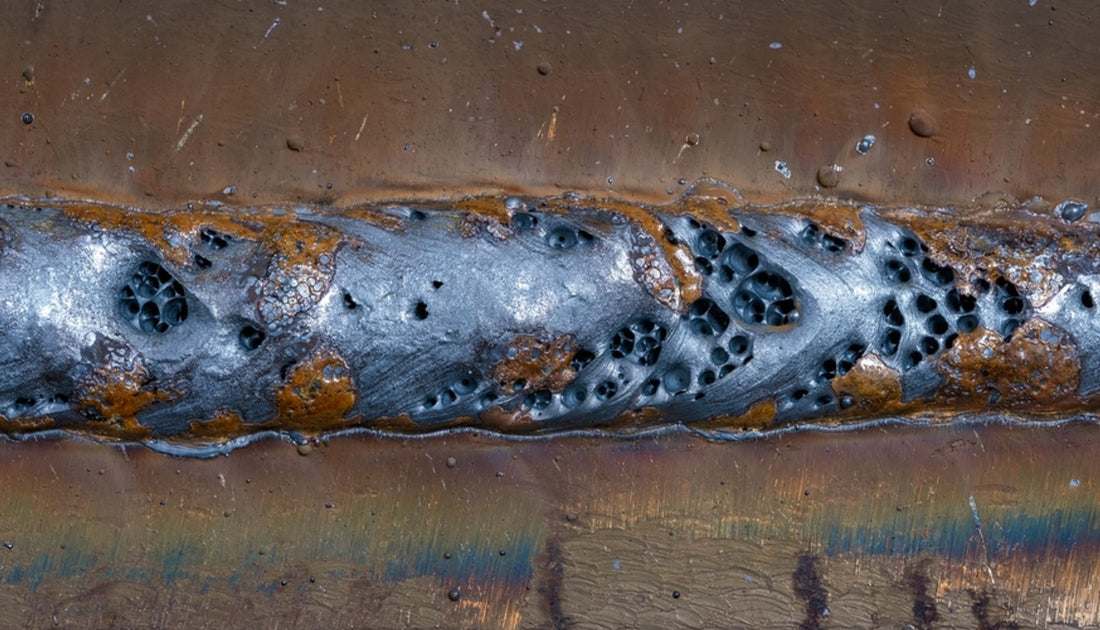
Another frequent offender behind porosity is the existence of pollutants externally of the base steel, such as oil, grease, or corrosion. When these contaminants are not properly eliminated prior to welding, they can vaporize and end up being trapped in the weld, causing defects. Moreover, using dirty or damp filler materials can present impurities right into the weld, adding to porosity problems. To minimize these common reasons for porosity, detailed cleaning of base steels, appropriate protecting gas selection, and adherence to optimum welding specifications are vital practices in achieving high-grade, porosity-free welds.
Impact of Porosity on Weld Top Quality

The presence of porosity in welding can significantly endanger the architectural stability and mechanical buildings of bonded joints. Porosity develops gaps within the weld steel, compromising its total toughness and load-bearing ability.
Welds with high porosity levels often tend to display lower effect stamina and decreased ability to deform plastically prior to fracturing. Porosity can restrain the weld's capacity to successfully transmit forces, leading to early weld failure and possible safety threats in critical structures.
Ideal Practices for Porosity Prevention
To enhance the structural integrity and quality of welded joints, what details steps can be applied to reduce the event of porosity during the welding process? Porosity prevention in welding is vital to ensure the honesty and strength of the final weld. One effective technique appertains cleansing of the base steel, removing any type of impurities such as corrosion, oil, paint, or moisture that could lead to gas entrapment. Making sure that the welding tools is in excellent condition, with tidy consumables and ideal gas flow rates, can also considerably minimize porosity. Furthermore, preserving a stable arc and regulating the welding parameters, such as voltage, existing, and take a trip speed, helps create a consistent weld pool that reduces the danger of gas entrapment. Utilizing the appropriate welding method for the specific material being welded, such as readjusting the welding angle and gun setting, can better stop porosity. Routine assessment of welds and instant remediation of any type of issues identified during the welding procedure are necessary techniques to stop porosity and produce high-grade welds.
Relevance of Appropriate Welding Methods
Applying appropriate welding strategies is extremely important in making certain the architectural honesty and high quality of welded joints, developing upon the foundation of effective porosity avoidance procedures. Extreme warm can lead to enhanced porosity due to the entrapment of gases in the weld swimming pool. Additionally, making use of the ideal welding criteria, such as voltage, present, and travel speed, is vital for achieving audio welds with marginal porosity.
In addition, the choice of welding process, whether it be MIG, TIG, or stick welding, must straighten with the details needs of the task to make sure optimal outcomes. Appropriate cleansing and prep work of the base steel, along with selecting the right filler material, are likewise vital parts of competent welding methods. By sticking to these best practices, welders can minimize the risk of porosity formation and create high-grade, structurally audio welds.
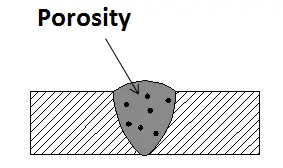
Testing and Quality Control Steps
Quality control procedures play a critical duty in verifying the integrity and dependability of welded joints. Checking procedures are necessary to find and avoid recommended you read porosity in welding, guaranteeing the stamina and sturdiness of the end product. Non-destructive screening approaches such as ultrasonic screening, radiographic screening, and aesthetic examination are frequently employed to recognize possible issues like porosity. These strategies enable the evaluation of weld high quality without jeopardizing the integrity of the joint. What is Porosity.
Performing pre-weld and post-weld inspections is additionally important in maintaining quality assurance requirements. Pre-weld examinations include verifying the products, equipment settings, and sanitation of the work area to stop contamination. Post-weld assessments, on the other hand, assess the final weld for any issues, including porosity, this contact form and validate that it fulfills defined criteria. Applying a detailed top quality control plan that consists of thorough screening treatments and inspections is paramount to reducing porosity concerns and guaranteeing the general top quality of welded joints.
Conclusion
In verdict, porosity in welding can be a typical problem that influences the top quality of welds. By determining the usual sources of porosity and carrying out finest methods for prevention, such as correct welding methods and screening steps, welders can guarantee premium quality and trusted welds. It is necessary to focus on prevention approaches to decrease the additional reading event of porosity and keep the stability of welded frameworks.